Well, It took me about 45min. The car was already on jackstands. I don't have a track locator so when the rear end moved after unbolting the first control arm the double adjustability came in handy right from the get go!
I bolted the front in and put the spring (Todd's old 88gt springs) on top. Then I jacked up the control arm into the axle housing (using a rag on the jack of course. Didn't want to scratch these new puppies
). Once in the housing I adjusted the control arms out until the bolt hole lined up. After I put the bolts in I adjusted the control arms back in to all the way which is right at 17.5" which is stock length. I repeated that procedure on the other side. I did still have to put a screw driver in the hole and persuade it to line up a bit, but it was a piece of cake!
In the first pic you will see the spring to the left with more of a shine is the 88GT spring. The spring on the right is the SN95 spring. The 88Gt spring is slightly taller. I feel really good about this install and I know deep down that it's going to work out for the better. It just feels right! :rock:
Note: I left everything loose until the suspension is loaded. Then I'll go back and tighten everything down.
88Gt spring left / 95 SN95 spring right
I bolted the front in and put the spring (Todd's old 88gt springs) on top. Then I jacked up the control arm into the axle housing (using a rag on the jack of course. Didn't want to scratch these new puppies

In the first pic you will see the spring to the left with more of a shine is the 88GT spring. The spring on the right is the SN95 spring. The 88Gt spring is slightly taller. I feel really good about this install and I know deep down that it's going to work out for the better. It just feels right! :rock:
Note: I left everything loose until the suspension is loaded. Then I'll go back and tighten everything down.
88Gt spring left / 95 SN95 spring right


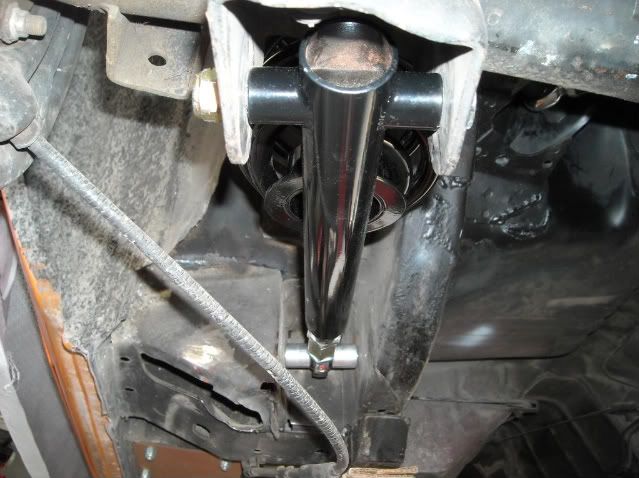

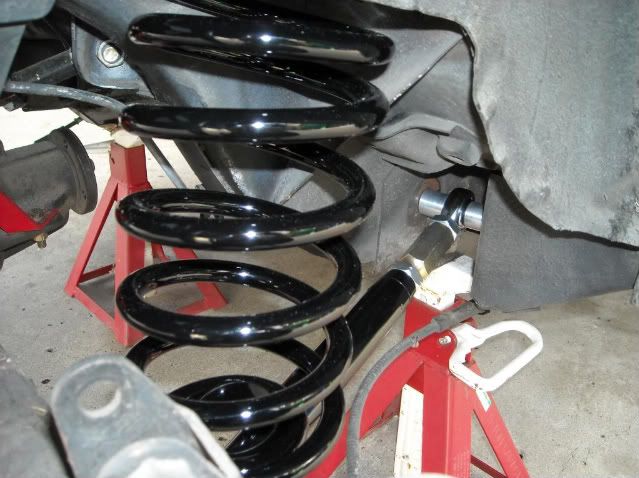
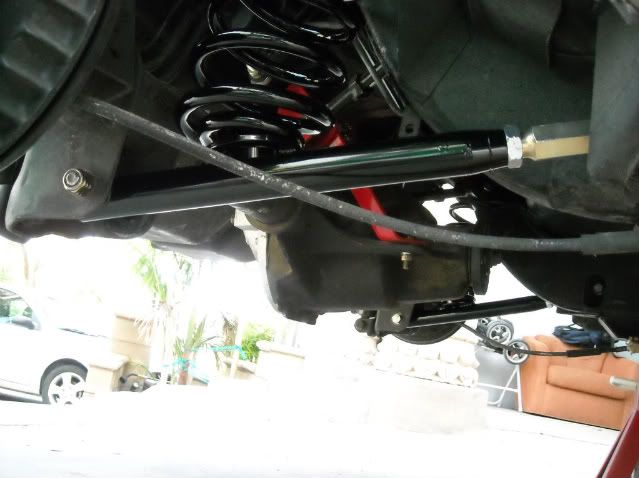